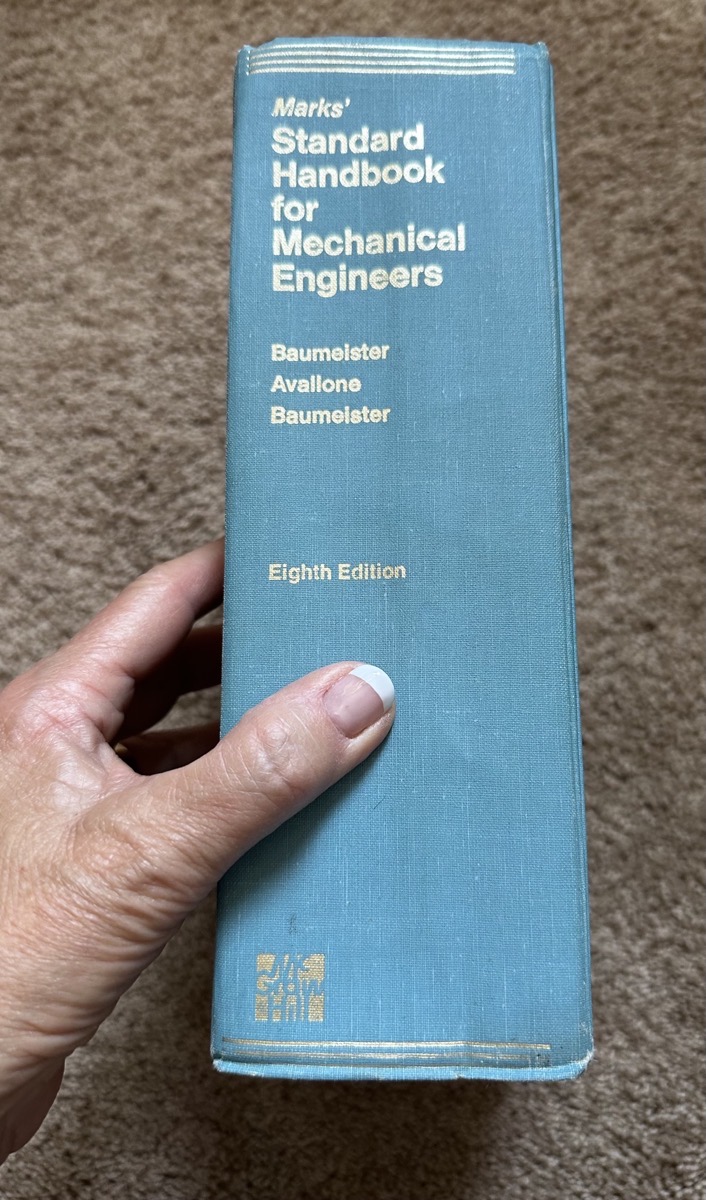
It’s the time of year when the wild and unsubstantiated rumors about the new iPhone and Apple Watch are resolving into less wild and more substantiated rumors. In less than two weeks we’ll know what’s coming but the frenzy doesn’t slow down just because we’ll know soon.
One of the rumors is that Apple is going to eschew the stainless steel rim around the iPhone in favor of titanium. The Apple Watch Ultra comes in titanium but they don’t tell us which titanium. They only call it “aerospace-grade titanium.”
As a mechanical engineer in my day job for many years, I had the opportunity to choose materials to build things, so I know a little bit about why you’d make the tradeoff between steel, aluminum, and titanium. And better yet, I feel the need to share a bit of what I know.
Metals have a few properties to consider. In military devices like what I worked on that often went on aircraft, and in commercial electronics like iPhones, a big consideration is trying to make the devices lighter without sacrificing strength.
Weight is a function of how dense a material is, which is mass divided by volume. In metric units, we use grams per cubic centimeter. So let’s take a look at three materials and see which one we should use to make our proposed iPhone, based entirely on density so it won’t weigh down our purses so much.
We’ll compare three metals:
- Aluminum alloy which is a blend of aluminum with a dash of magnesium and silicon. For the nerdy amongst you, I’ll be using 6061-T6 specifically, but don’t worry your pretty little head about that if you’re not into materials specifications. I like this one because I actually remember specifying 6061 on my drawings back in the early 1980s.
- Stainless Steel — in this case, I’ll be using 301 for the properties.
- Titanium Ti-6Al-4V where the “Al” and “V” stand for Aluminum and Vanadium to make the alloy. Apple simply says “aerospace-grade titanium”, and the ASM folks say it’s good for “Blades, discs, rings, airframes, fasteners, components. Vessels, cases, hubs, forging, and biomedical implants.”
My main source of data for this exercise is from asm.matweb.com. ASM stands for the American Society for Materials, and I bet their conferences are a hootin’ good time.
I’d also like to point out that I cross-referenced as much as I could from the book my father gave me shortly after I graduated from college. The book he gave me (when my mother wanted to give me a dress (can you imagine?)) is Marks’ Standard Handbook for Engineers, 8th edition published in 1978. The specific table I used for cross-referencing the materials information is on page 6-11. I wasn’t able to cross-reference as much as I’d hoped as materials have advanced since 1978!
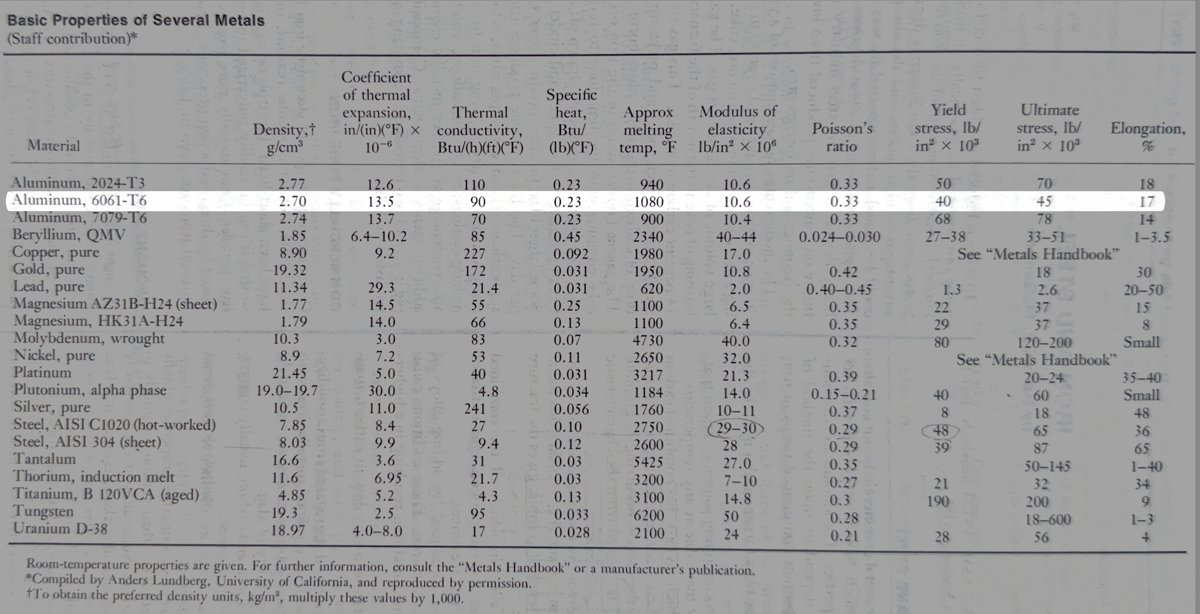
Okay, with my sources duly referenced, let’s get into the good stuff.
If we look at the density alone of the three materials we’ve chosen, we find that the aluminum alloy has the lowest density at 2.7 grams per cubic centimeter. Steel comes in at over 8, and titanium comes in at 4.4.
Clearly, we should use aluminum for our fantasy iPhone because it has the lowest density, right? Slow down, Skippy, there’s more to the story than just the density. What if Aluminum isn’t as strong as the other contenders for the same volume? Don’t you want your iPhone’s frame to be strong?
One measure of strength is Ultimate Tensile Strength. Sounds like something one of those shows with people fighting for physical supremacy should use, doesn’t it? Strength is measured in Freedom Units in psi or pounds per square inch, but in the rest of the world, it’s measured in megapascals. A Pascal is one Newton per meter squared, and a Newton is one kilogram-meter per second squared. I bet that’s more than you wanted to know, isn’t it? Sorry, couldn’t help myself. Let’s get back to the plot at hand.
How do our three materials measure up in the Ultimate Tensile Strength contest?
Our previous fan-favorite, aluminum, comes in at a paltry 310 megapascals, while stainless steel comes in at a strong 862 megapascals. Don’t count titanium out yet though, it finishes with a winning 950 megapascals. It’s more than triple the Ultimate Tensile Strength of aluminum!
Now we have a quandary. While aluminum has the lowest density, titanium is the clear winner when it comes to Ultimate Tensile Strength. How do we decide?
The answer is to calculate the Specific Strength. You’re going to absolutely love this one. The unit for Specific Strength is kilonewton-meter per kilogram. I am not making this up. While the units are clearly getting out of control, calculating Specific Strength is trivial. We simply divide our old friend Ultimate Tensile Strength by density.
Our three contestants, aluminum, steel, and titanium come in with these final stats for Specific Strength:
- Stainless Steel at 107 kN-m/kg
- Aluminum alloy 6061-T6 comes in second at 115 kN-m/kg
- Titanium wins the battle for the materials at over 214 kN-m/kg
Now that we know titanium is the clear winner in the materials battle, what does this really mean?
If Apple chose Titanium for the next iPhone, they could keep the exact same frame design and swap out the heavy, but relatively strong, stainless steel for titanium. Since titanium is less dense, the same-sized frame would be much stronger.
Alternatively, they could choose to make the frame thinner, while maintaining the same strength.
The last thing to take into consideration is cost. Titanium is a lot more expensive than stainless steel for a couple of different reasons.
Titanium is rarer than the elements required to make stainless steel, so the material costs alone would make the phone more expensive. Titanium is also much harder to machine. Machining the same iPhone frame out of titanium would increase the cost of making the device. We’ve heard rumors of an increase in the base price, and this could be one of the reasons why.
I don’t know what Apple will do with the next iPhone but I hope you enjoyed my little lesson on why titanium might be in our future for more than the Apple Watch Ultra.
Hello Alison, excellent article. I am thinking the thickness of the frames might be governed by stiffness requirement and not strength. So it might make sense to compare the modulus of elasticity and not just the ultimate strength. Also, I would imagine the design for the frames would be restricted to Allowable Stress Design (ASD) and not Ultimate Limit State, so it might make sense to compare the Yield Strength and not the Ultimate Strength.
Again, excellent article. Feels great to have the Mechanical/Structural Engineering community represented in the Apple world.
Hey Darshan – nice to meet a fellow mechanical engineer here too. I thought about using stiffness as a metric too, but I figured I was getting pretty nerdy as it was. I used to design small steering mirrors (<2” across) that were steered using tiny voice coil actuators, on four sides. The mirrors rotated on a flex pivot machined out of titanium. Fun stuff!
Thank you for this article. This makes me wish I’d become a mechanical engineer like my grandfather. You have an excellent writing style, too.
Given that past iPhones may have suffered from deformations (“Bendgate”), might it be useful to examine rigidity as well? I believe that would be measured in Young’s modulus? While it may be beyond my powers to calculate, Bard says what follows. While the assessment makes sense to me, the elastic modulus values do not seem to support the conclusion:
[Bard Quote] … The relative rigidity of aluminum alloy 6061-T6, stainless steel 301, and titanium Ti-6Al-4V is as follows:
Titanium Ti-6Al-4V > Stainless steel 301 > Aluminum alloy 6061-T6
This means that titanium is the most rigid material, followed by stainless steel, and then aluminum alloy.
Here is a table of the elastic modulus of each material:
| Material | Elastic modulus (GPa) |
|—|—|—|
| Aluminum alloy 6061-T6 | 70 |
| Stainless steel 301 | 200 |
| Titanium Ti-6Al-4V | 115 |
…[Unquote]